News & Media
Started shipping core “Thermal Shield” of ITER, developed by Korea, to France
- NameKFE
- Date2020-06-05
- Hit1,797
Pre-assembly of 6th sector of vacuum vessel thermal shield is completed in August, 2018
After the completion of the final inspection of the first product of the thermal shield (TS), which is a domestically produced procurement item for the construction of an ITER device and is one of the core parts of the 'ITER', ITER Korea (KO-DA) of the National Fusion Research Institute (NFRI), had it transported in September 2019, through the port of Busan, to the Cadarache region in France, the site of ITER construction.
The TS is a device that prevents the radiation heat transferred from the vacuum vessel in which ultra-high temperature plasma is generated in a nuclear fusion reactor and other room-temperature structures from being transmitted to a superconducting magnet operating at an extremely low temperature (-269°C). It is largely divided into the Vacuum Vessel Thermal Shield (VVTS) and Cryostat Thermal Shield (CTS). When the TS is assembled , the total height and diameter both reach 25m and the total weight is about 900 tons. This thermal shield is a procurement product that Korea is 100% responsible for, from design to manufacturing.
ITER Korea has been developing and manufacturing the TS since 2014, in cooperation with SFA Co. Among all parts, the 6th sector of the VVTS and the lower cryostat thermal shield (LCTS) cylinder were the first to be manufactured and were shipped to the ITER construction site after the factory acceptance test.
The VVTS, installed between the vacuum vessel and the superconducting magnet, is made of nine sectors bydividing the entire 360-degree donut shape into 40-degree intervals. The 6th sector was made of 31 panels,and in August 2018, the sector was preassembled according to its design and the suitability of the thermalshield was successfully validated and verified. This means that a sophisticated device manufacturingtechnology has been successfully implemented to allow only 2mm tolerance of VVTS, which is 12m in height(tolerance between design and product). Subsequently, the re-dissasembled thermal shield panels weresubjected to silver plating, the final stage of production, by May 2019. Silver plating, the core technology of TSmanufacturing, serves to block the radiation heat transferred to the superconducting magnet by lowering theemissivity of the TS. To this end, SFA completed a silver plating facility consisting of 11 of the world's largestlarge-sized steel plating baths, and succeeded in implementing uniform silver plating with a thickness of 8 to10㎛ on the surface of a large thermal shield through plating tests for one year.
“Thermal shields that are assembled with a total of 600 panels and 70,000 bolts require meticulous design and manufacturing because they have very complicated interfaces with adjacent systems inside the Tokamak," said Her Nam Il, Director of the Tokamak Plant Engineering Division of ITER, Korea, who has led the ITER thermal shield development. "As a result of working together as one team with domestic partners and ITER organization to overcome various technical challenges, we were able to successfully manufacture an ITER thermal shield," he added.
The first ITER thermal shield product, which began to be shipped by sea, arrived at the ITER construction site in the Cadarache region in southern France in mid-October 2019; the remaining thermal shields currently in production will be completed by October 2020 and procurement will finally be completed by early 2021.
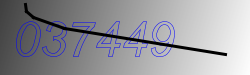
보안문자를 입력 후 확인 버튼을 누르세요.